While Matt's car was in process I also had some other projects come through the shop.
A few months back this M3 came in to get a 6spd conversion (from SMG). He had a bunch of warning lights on and was complaining about poor shifting and thought it had a SMG failure. I diagnosed it to just be missing a fuse in the DSC which was causing the poor shift quality. After that was fixed he was delighted with the outcome and we focused our attention else where. I did the vanos lock down a while back, but we also found a couple cracks in the RACP (rear axle carrier panel or sometimes called subframe).


RF mount crack.

Stop drilled and welded.

Ground down and ready for plates.

My goto, CMP Auto Engineering plates going on.
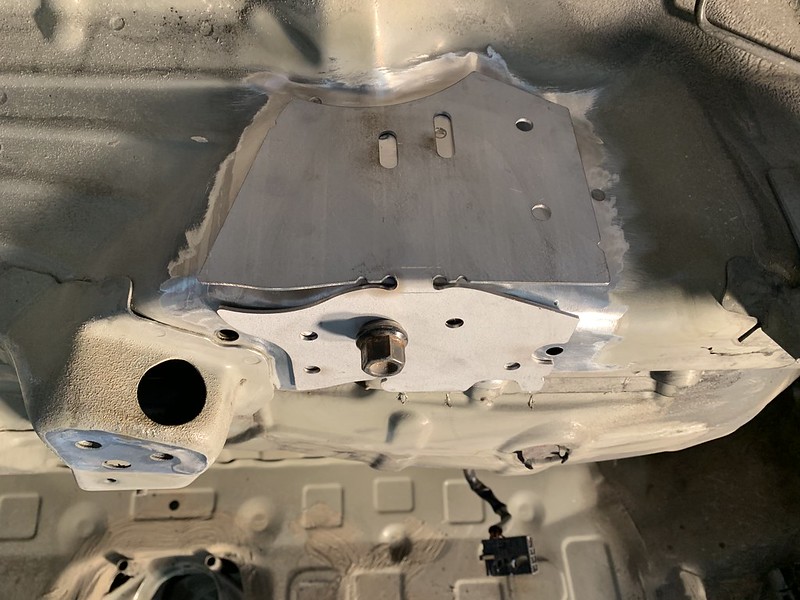
Formed and burned in.

Primed.

And undercoated.

CMP RTAB/J

Subframe bushings were replaced with BMW bushings along with a new Guibo.

And getting lined up.
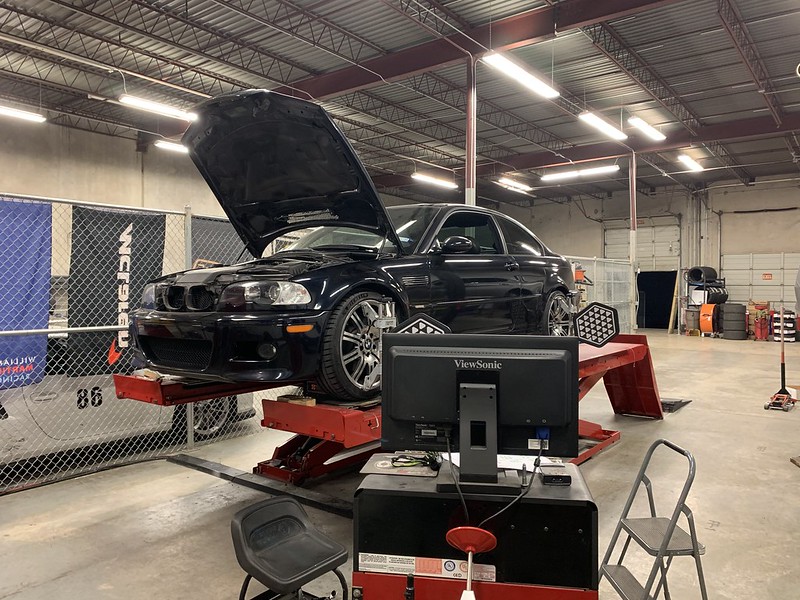
Guillaume brought in his carbon black M3 for replacement of a final drive mounting bushing. When I was inspecting the car it was found he had quite a few cracks in his RACP, so our bushing replacement turned into a full blown RACP repair. We did the usual, CMP plates, RTAB/J, Guibo, diff bushing and brake lines all around.


RTAB's dead.

Crack in drivers side arch.
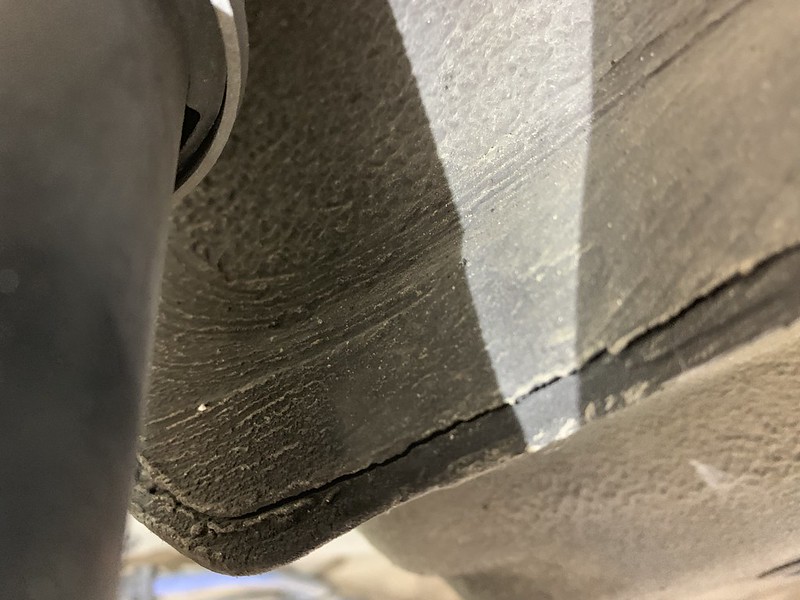

Popped spot welds.
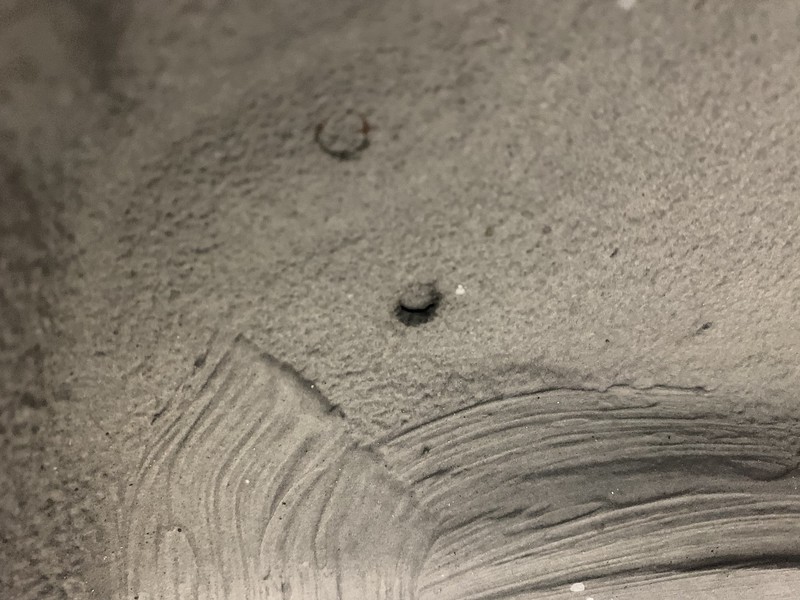
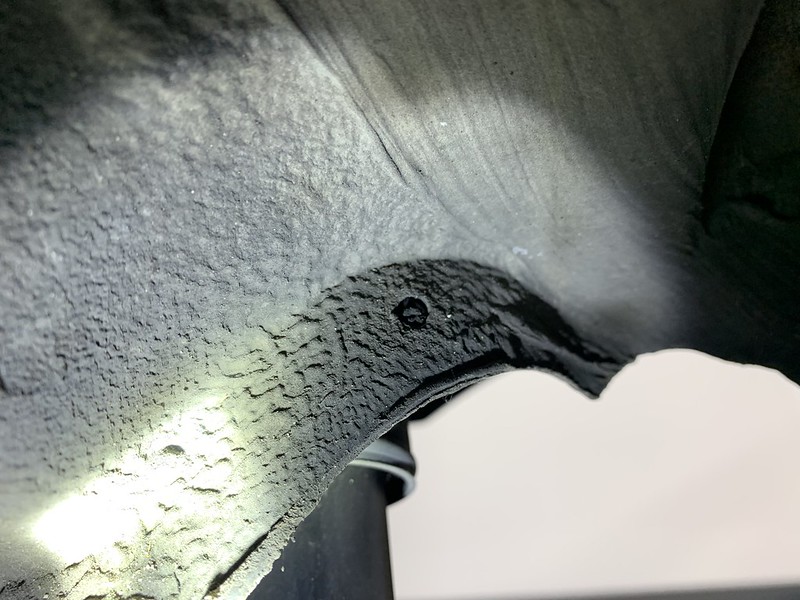
Cracks in the subframe attachment areas.


All disassembled and prepped.


Welded and seam sealer going on.

And back together and getting lined up.

Mike brought in his SpecE46 for a little bit of strut tower modification.
His negative camber was limited due to the struts hitting the strut tower opening. The passenger side had already been opened up, but the drivers side was stock. The strut towers were like you would expect from a racecar, they had lived a tough life, so I started by getting them all flattened out properly. He already had reinforcement plates installed but I riveted them to the tower (just to keep them from moving during servicing the alignment, struts, etc). Then traced out where I needed to cut and let the metal fly, the goal being to only remove enough material to not limit adjustment and still reach all the mounting hardware. I cleaned up some of the wiring and clearance the B+ terminal to allow access with everything assembled. Hopefully he can get the camber he needs otherwise we'll have to slot the factory bolt openings for more.


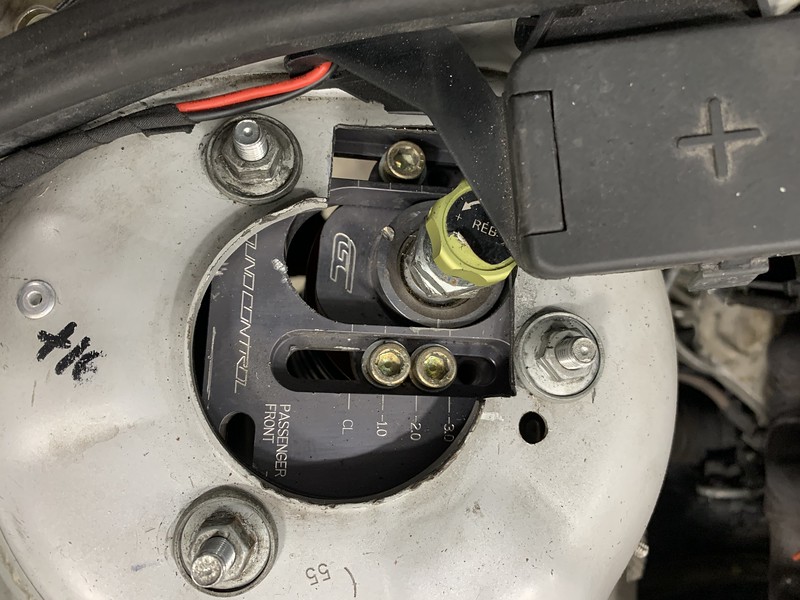
A few months back this M3 came in to get a 6spd conversion (from SMG). He had a bunch of warning lights on and was complaining about poor shifting and thought it had a SMG failure. I diagnosed it to just be missing a fuse in the DSC which was causing the poor shift quality. After that was fixed he was delighted with the outcome and we focused our attention else where. I did the vanos lock down a while back, but we also found a couple cracks in the RACP (rear axle carrier panel or sometimes called subframe).


RF mount crack.

Stop drilled and welded.

Ground down and ready for plates.

My goto, CMP Auto Engineering plates going on.
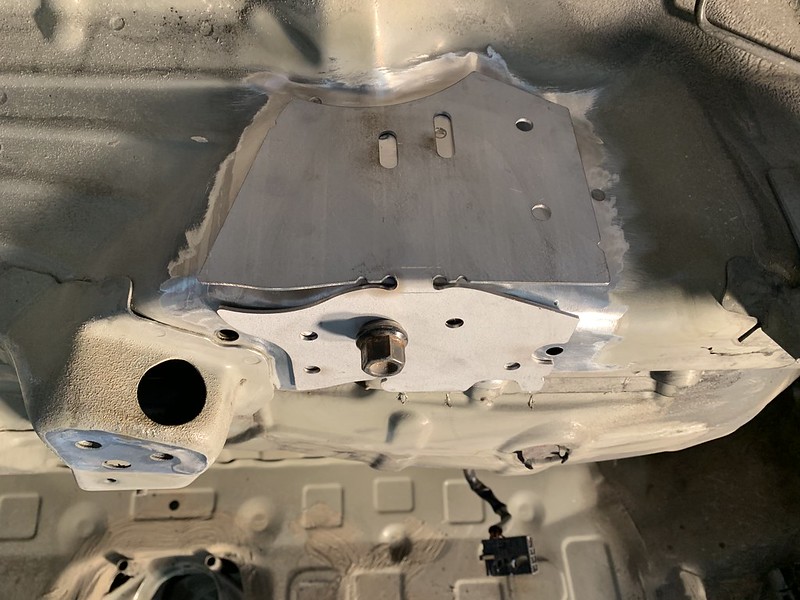
Formed and burned in.

Primed.

And undercoated.

CMP RTAB/J

Subframe bushings were replaced with BMW bushings along with a new Guibo.

And getting lined up.
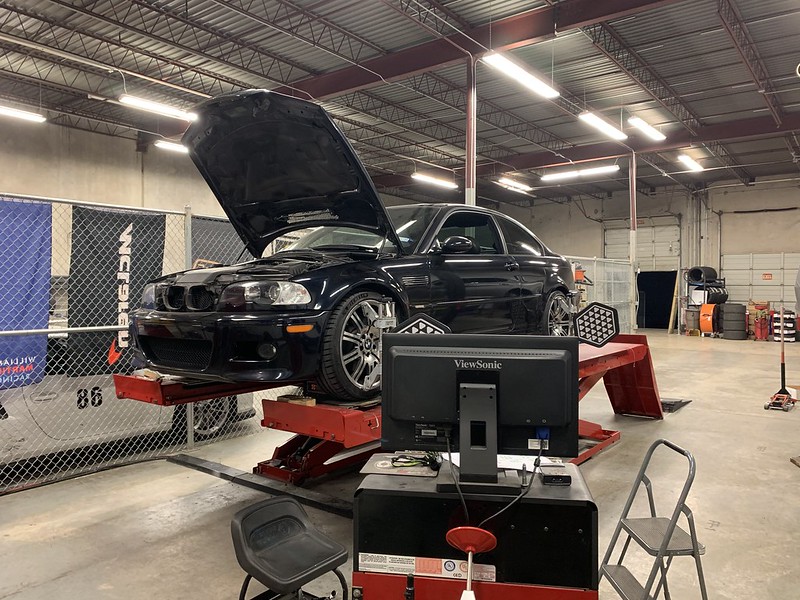
Guillaume brought in his carbon black M3 for replacement of a final drive mounting bushing. When I was inspecting the car it was found he had quite a few cracks in his RACP, so our bushing replacement turned into a full blown RACP repair. We did the usual, CMP plates, RTAB/J, Guibo, diff bushing and brake lines all around.


RTAB's dead.

Crack in drivers side arch.
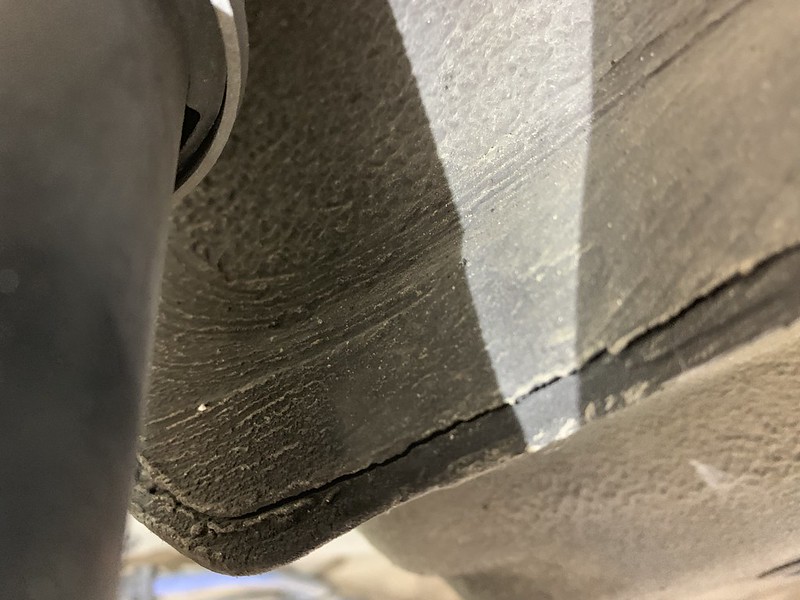

Popped spot welds.
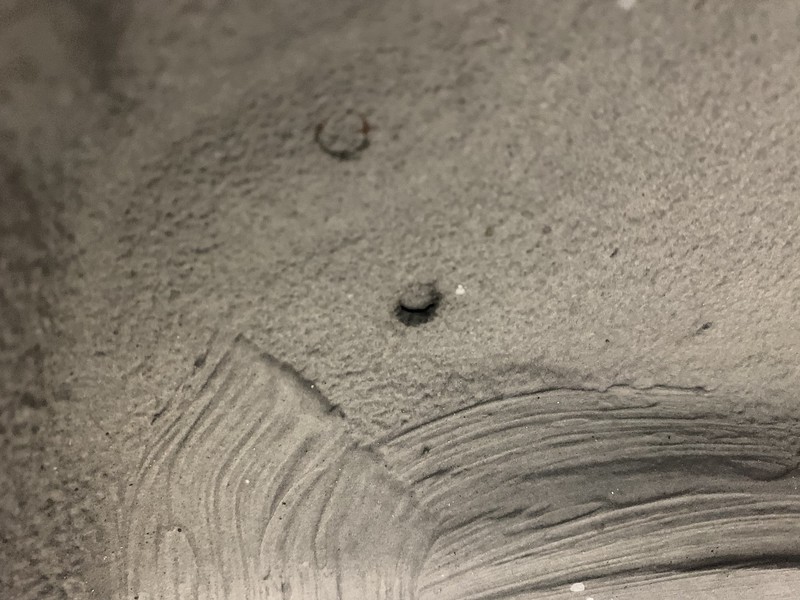
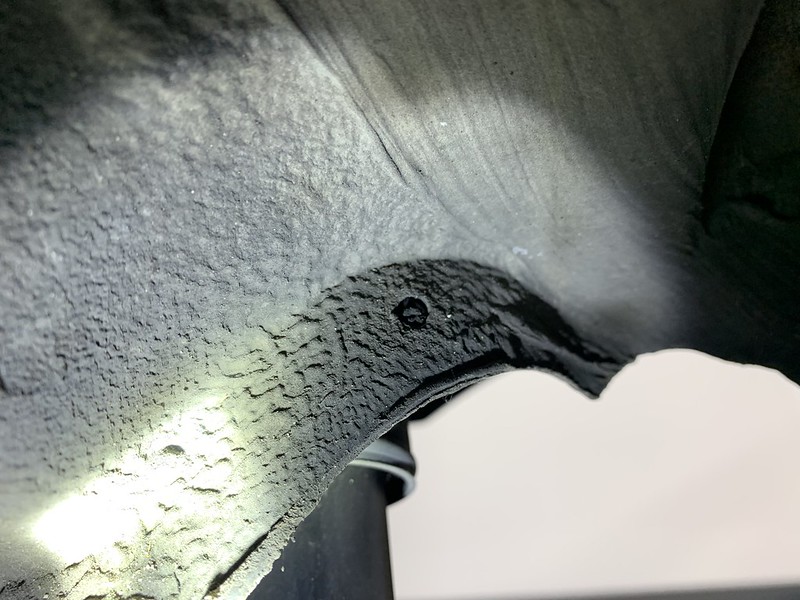
Cracks in the subframe attachment areas.


All disassembled and prepped.


Welded and seam sealer going on.

And back together and getting lined up.

Mike brought in his SpecE46 for a little bit of strut tower modification.
His negative camber was limited due to the struts hitting the strut tower opening. The passenger side had already been opened up, but the drivers side was stock. The strut towers were like you would expect from a racecar, they had lived a tough life, so I started by getting them all flattened out properly. He already had reinforcement plates installed but I riveted them to the tower (just to keep them from moving during servicing the alignment, struts, etc). Then traced out where I needed to cut and let the metal fly, the goal being to only remove enough material to not limit adjustment and still reach all the mounting hardware. I cleaned up some of the wiring and clearance the B+ terminal to allow access with everything assembled. Hopefully he can get the camber he needs otherwise we'll have to slot the factory bolt openings for more.


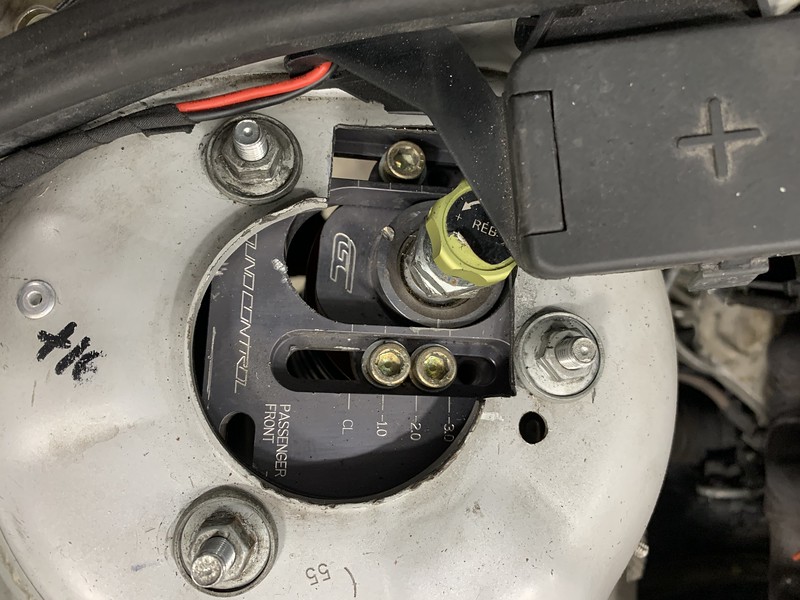

Comment