I had this as a post on the old M3forum.net. but seems fun enough to repost here.
Back in 2014 I was in Italy, and thought it would be fun to stop by SuperSprint. They don't normally do tours, but I had been talking to them enough over the years that they took me around anyway.
*Disclaimer* Photos were being snapped quickly as I moved throughout the facility, and were taken with an iPhone in 2014. So... set your quality expectations accordingly.
Firstly, everywhere outside of cities the driving was amazing. Screen shot along our nav route to SS:
Arrival:
From the front gates you get the impression it is a rather small facility. That is not correct.
file_zpsa1da0bc1.webp
file_zpsd4494315.webp
Research and Development:
First stop was the R&D facility. This is where they bring in fitment cars for the initial mock up, dyno test the prototype products, and design the jigs for future production(faces blanked out in all photos). Sadly, I forgot to snag a photo of the dyno, but it is an impressive unit. 4WD capable that measures both crank and wheel HP(using engine rundown to calculate drivetrain loss), with sensors for exhaust pressure, exhaust temp, fan setups for front and rear engines, water sprayers for FI intercoolers, and so on and so forth. Extremely impressive unit.
05ad2235-c15b-4f6f-abd0-b1ed23a55408_zpsa9482275.webp
F30 335i currently being mocked up. As they discovered that it shares the same floor pan as the F8x M3, they were able to run a true dual pipe setup instead of the stock mono pipe. Please note that this is a fitment prototype.
file_zps43f23970.webp
Jigs being fabbed up for later use.
file_zps73f66a58.webp
Storage:
Stepping out of the R&D facility takes us to metal stock storage, and one of many jig storage facilities. As Supersprint has been around since 1955, and both makes exhausts for nearly every slightly performance related vehicle and keeps them around, there is a near endless amount of jigs. Pretty much any place they have extra room, they store jigs.
As all Supersprint exhaust pieces are made from 304 stainless, which does not rust, they are free to store all their pipe outside. Depending on application(race vs street), pipe thickness can range from 1mm to 1.5mm, as the tradeoff of weight vs strength is balanced.
file_zps3cec8202.webp
file_zpsb61857a6.webp
First jig storage sighting. I won't be posting all the photos of jigs as there are a ton.
file_zps82f14e06.webp
Jigs are all individually catalogued and labeled for easy later access.
file_zps276f9bf4.webp
Some jigs are stored inside.
file_zpsc17a8405.webp
file_zps3b239d34.webp
And some jigs are stored outside. Jigs jigs jigs.

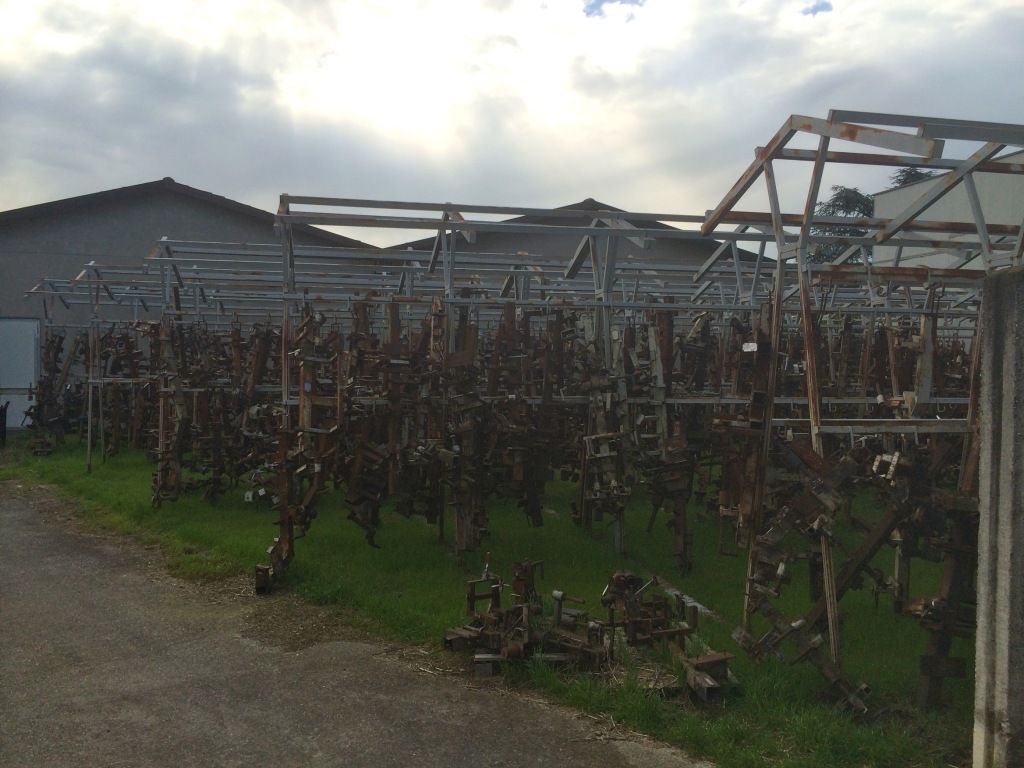
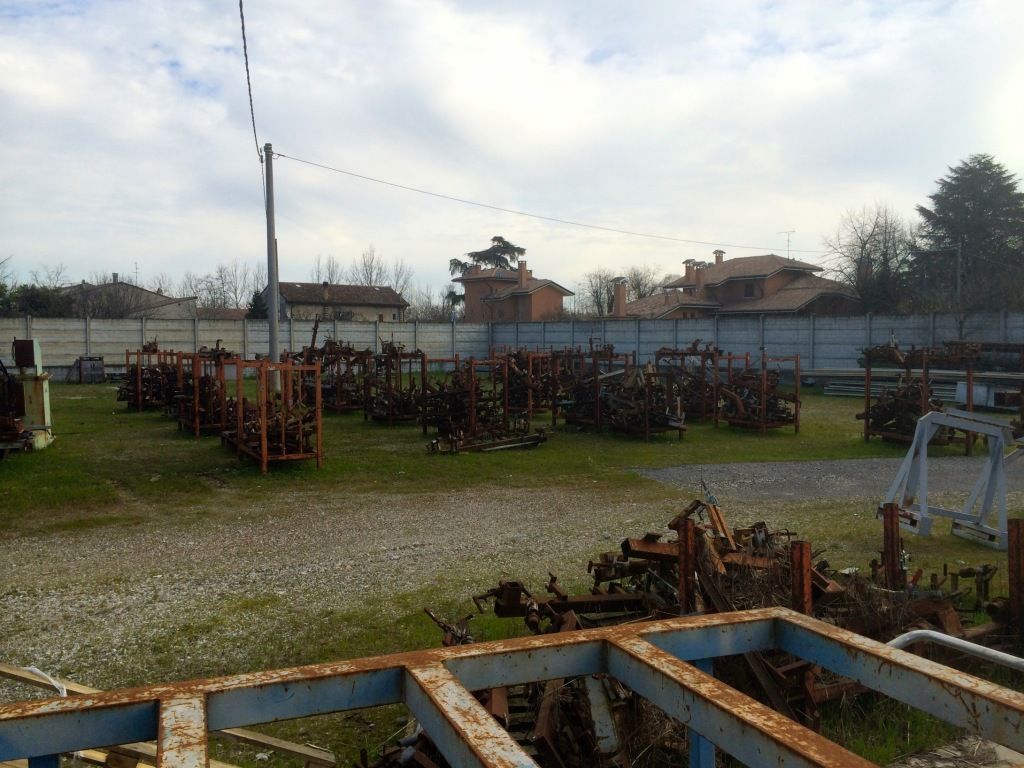
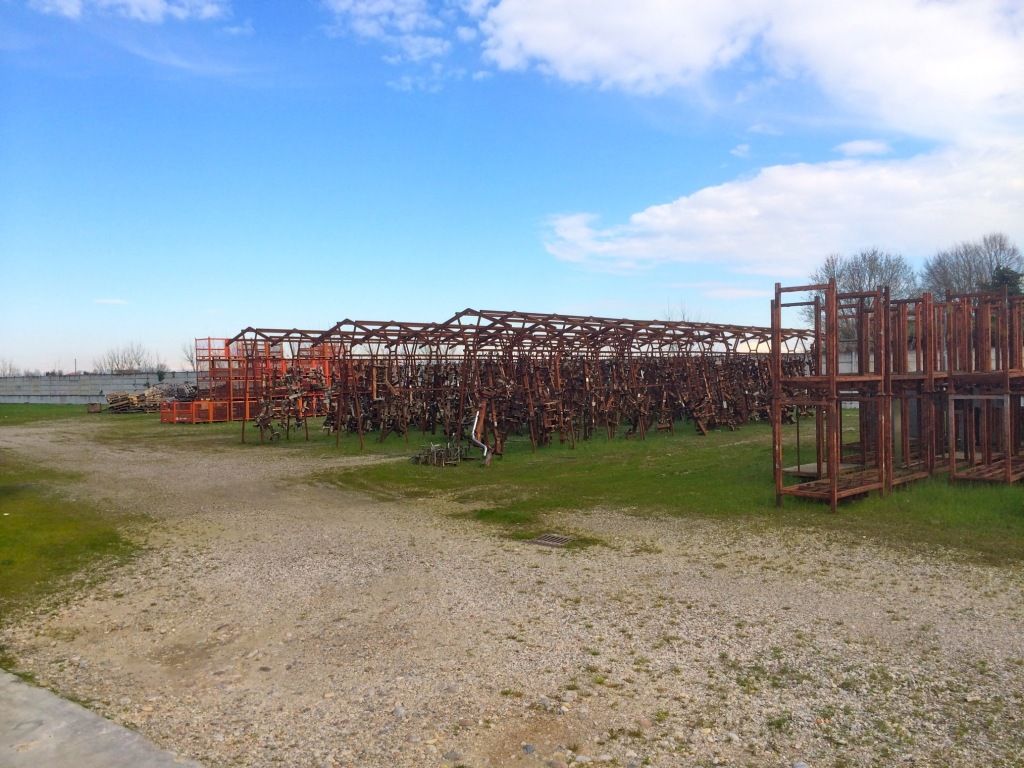
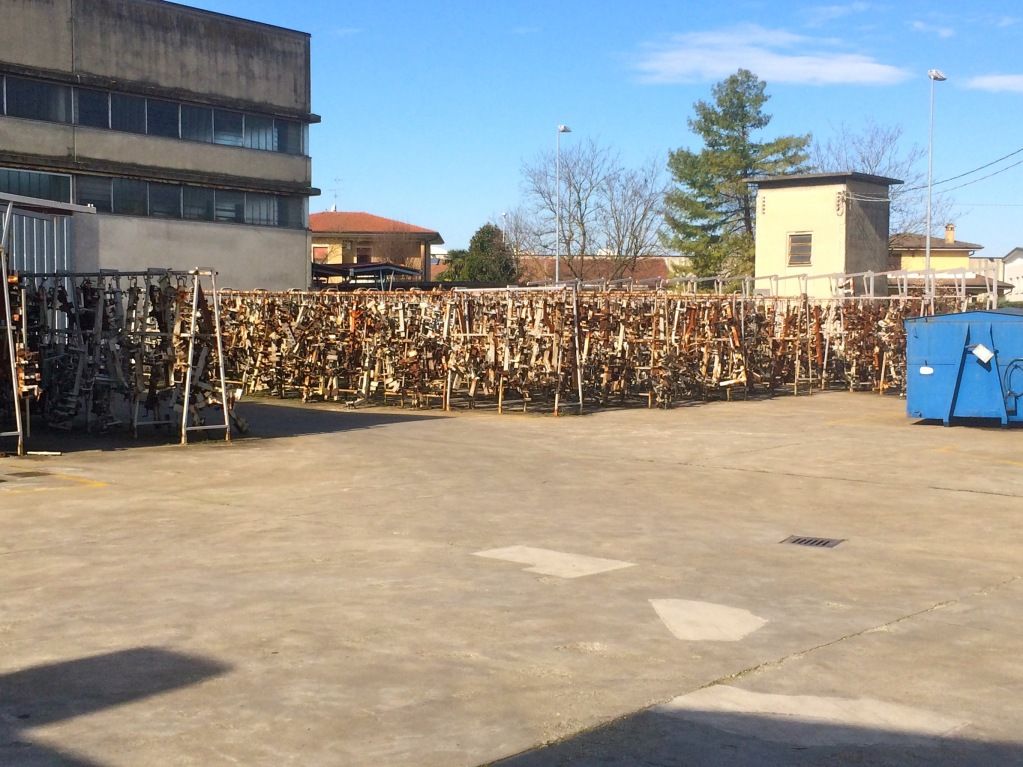
CNC mandrel bending:
file_zps1790cac0.webp
Confirming bend dims with the fixture:
file_zps9343d514.webp
Pieces randomly pulled for more intense quality checks:
file_zpsd3306772.webp
Welding
Spot weld robot:
file_zps3f6c74cb.webp
And then some Italians getting busy:
file_zps02ec63d7.webp
file_zpsbd1d24cf.webp
Header welding for a WRC car. Renault or Citroen(can't remember which) submitted their header design to Supersprint, who in turn built it to spec along with their own design which they felt was an improvement. Both were submitted back to the OE, who ended up picking Supersprint's design over their own.
file_zpsd726f81a.webp
file_zpsbd694aa9.webp
Finished product. The OE's WRC team needed a number of units. Because it is a WRC car, strength was favored over lightness, and as a result, 1.5mm pipe was used.
file_zpseac9ff09.webp
Batches of finished products ready to head onto the next stage.
file_zps25af3465.webp
One of the more interesting parts of QC, the negatives. These are the opposite ends of the flanges found on each Supersprint exhaust component, and each piece is tested with them to confirm a proper mating seal.
file_zpsee439dc6.webp
HJS race cat.
file_zpsf9042e68.webp
Just the tips:
file_zpsd7cc326c.webp
file_zpsabf7f89d.webp
Pressed Parts (merges):
file_zpse517d77c.webp
file_zpsbaacc76f.webp
Prototype 4-1 collector
file_zps88e7a2be.webp
file_zps109f97fa.webp
Cleaning and Shipping
Final stage for all items is heading over to the cleaning and shipping facility. It's hard to convey how large the initial plant was, but I can definitively say it is significantly larger than the Lamborghini factory I visited the previous day. This is also ignoring the large yards of even more jigs. I have visited other places like Fabspeed before, and frankly, they felt like a Meineke in comparison.
The cleaning and shipping building is actually a separate facility across the street, which itself is actually quite large.
file_zpse93dbaf3.webp
Exhaust components are hooked up to this rotisserie, where they are cycled through a number of cleaning bathes to remove process grime and work oils.
file_zpscf950053.webp
file_zpsbbf16e2f.webp
And packing:
file_zpsfd950bc6.webp
file_zps1a9d0e96.webp
file_zpsfdcdd232.webp
file_zps8c8876b6.webp
Back in 2014 I was in Italy, and thought it would be fun to stop by SuperSprint. They don't normally do tours, but I had been talking to them enough over the years that they took me around anyway.
*Disclaimer* Photos were being snapped quickly as I moved throughout the facility, and were taken with an iPhone in 2014. So... set your quality expectations accordingly.
Firstly, everywhere outside of cities the driving was amazing. Screen shot along our nav route to SS:
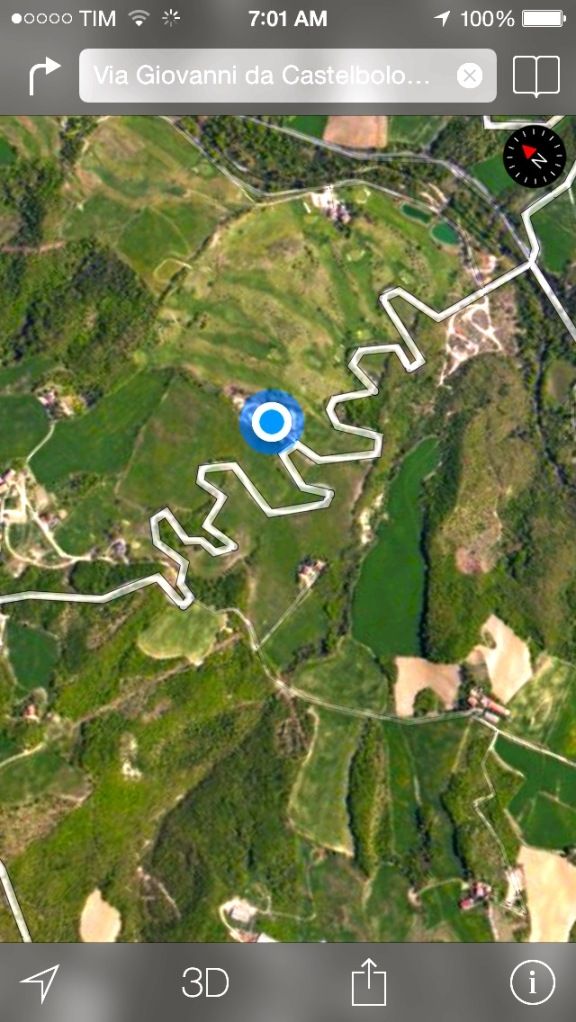
Arrival:
From the front gates you get the impression it is a rather small facility. That is not correct.
file_zpsa1da0bc1.webp
file_zpsd4494315.webp
Research and Development:
First stop was the R&D facility. This is where they bring in fitment cars for the initial mock up, dyno test the prototype products, and design the jigs for future production(faces blanked out in all photos). Sadly, I forgot to snag a photo of the dyno, but it is an impressive unit. 4WD capable that measures both crank and wheel HP(using engine rundown to calculate drivetrain loss), with sensors for exhaust pressure, exhaust temp, fan setups for front and rear engines, water sprayers for FI intercoolers, and so on and so forth. Extremely impressive unit.
05ad2235-c15b-4f6f-abd0-b1ed23a55408_zpsa9482275.webp
F30 335i currently being mocked up. As they discovered that it shares the same floor pan as the F8x M3, they were able to run a true dual pipe setup instead of the stock mono pipe. Please note that this is a fitment prototype.
file_zps43f23970.webp
Jigs being fabbed up for later use.
file_zps73f66a58.webp
Storage:
Stepping out of the R&D facility takes us to metal stock storage, and one of many jig storage facilities. As Supersprint has been around since 1955, and both makes exhausts for nearly every slightly performance related vehicle and keeps them around, there is a near endless amount of jigs. Pretty much any place they have extra room, they store jigs.
As all Supersprint exhaust pieces are made from 304 stainless, which does not rust, they are free to store all their pipe outside. Depending on application(race vs street), pipe thickness can range from 1mm to 1.5mm, as the tradeoff of weight vs strength is balanced.
file_zps3cec8202.webp
file_zpsb61857a6.webp
First jig storage sighting. I won't be posting all the photos of jigs as there are a ton.
file_zps82f14e06.webp
Jigs are all individually catalogued and labeled for easy later access.
file_zps276f9bf4.webp
Some jigs are stored inside.
file_zpsc17a8405.webp
file_zps3b239d34.webp
And some jigs are stored outside. Jigs jigs jigs.

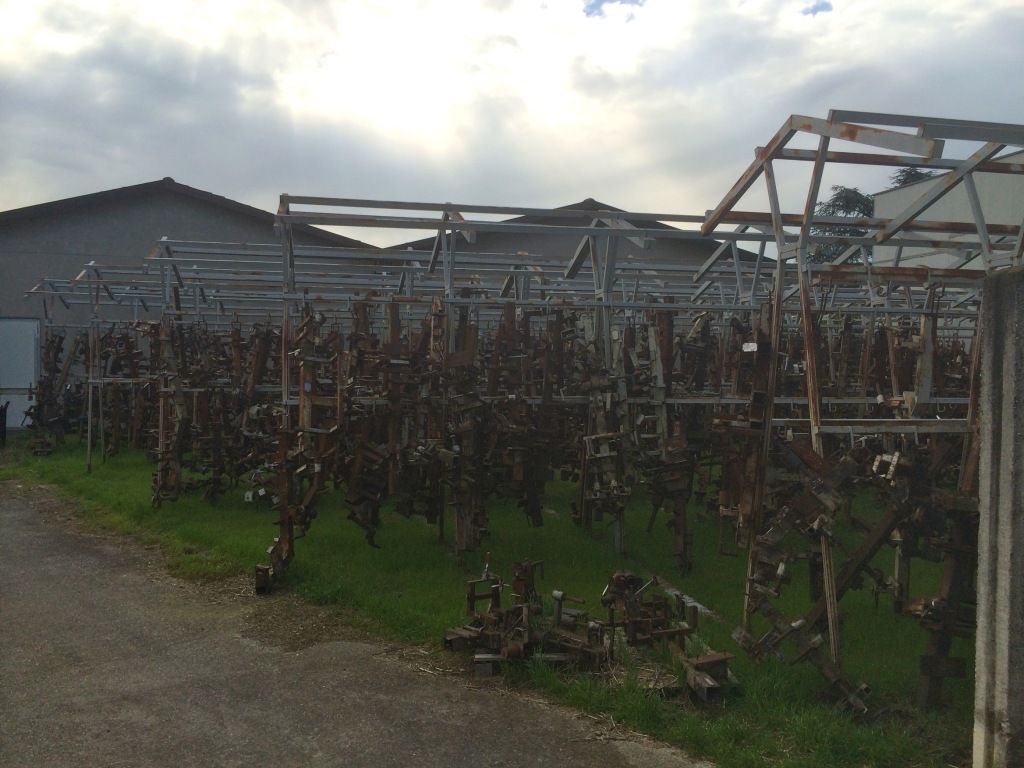
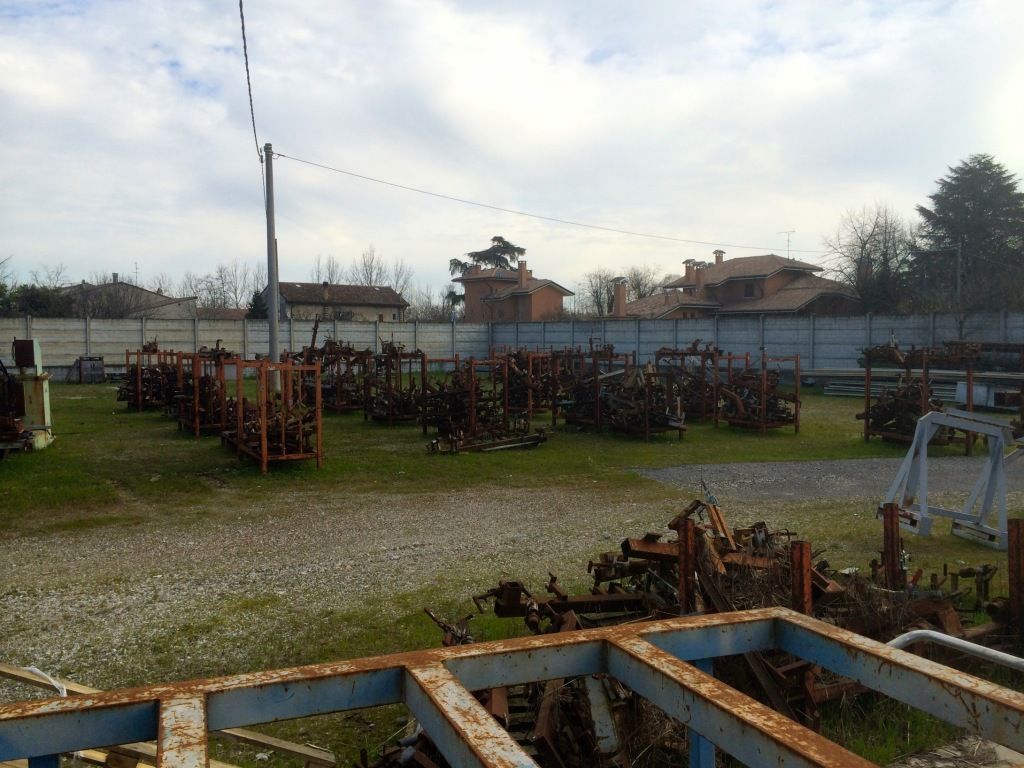
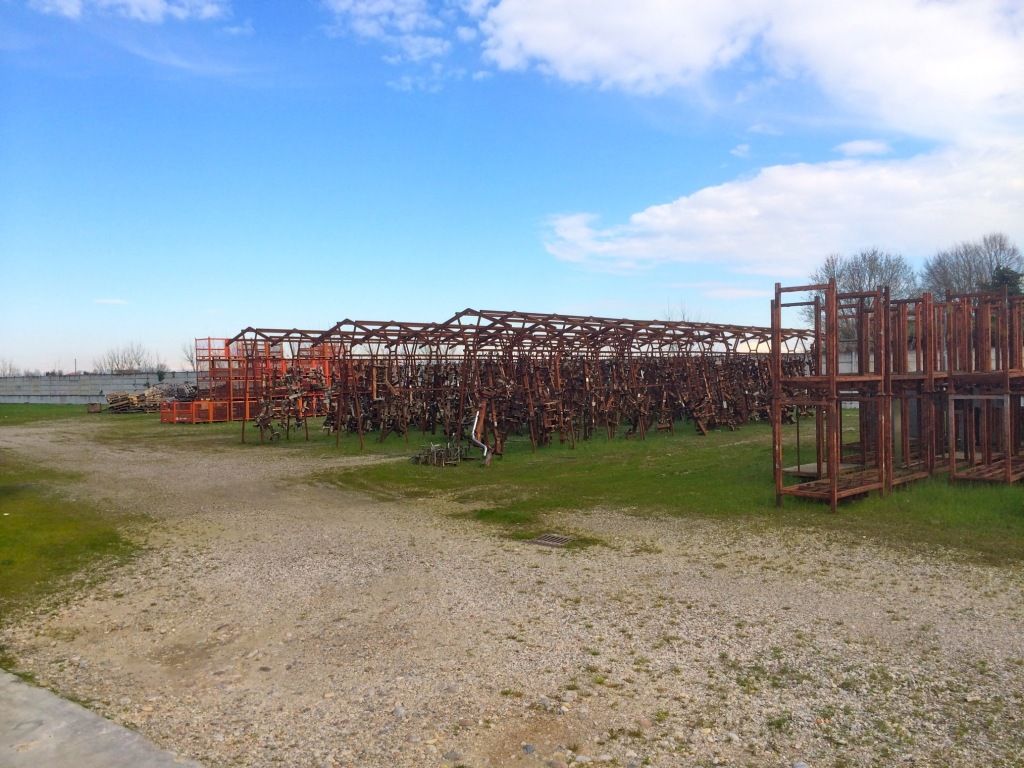
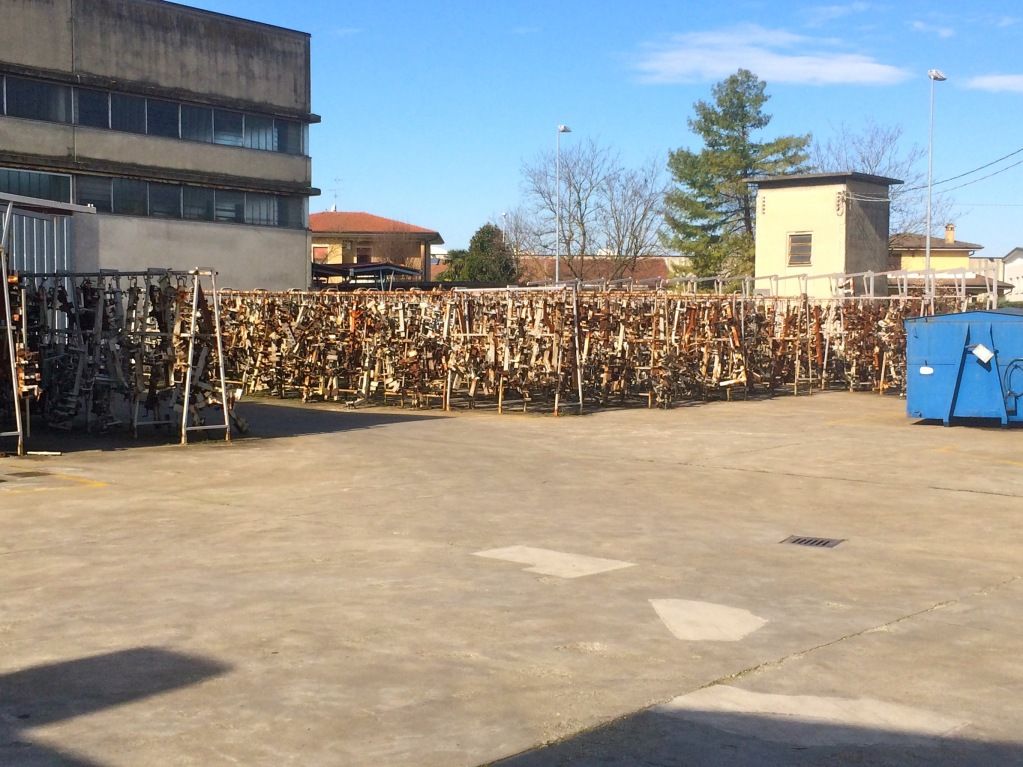
CNC mandrel bending:
file_zps1790cac0.webp
Confirming bend dims with the fixture:
file_zps9343d514.webp
Pieces randomly pulled for more intense quality checks:
file_zpsd3306772.webp
Welding
Spot weld robot:
file_zps3f6c74cb.webp
And then some Italians getting busy:
file_zps02ec63d7.webp
file_zpsbd1d24cf.webp
Header welding for a WRC car. Renault or Citroen(can't remember which) submitted their header design to Supersprint, who in turn built it to spec along with their own design which they felt was an improvement. Both were submitted back to the OE, who ended up picking Supersprint's design over their own.
file_zpsd726f81a.webp
file_zpsbd694aa9.webp
Finished product. The OE's WRC team needed a number of units. Because it is a WRC car, strength was favored over lightness, and as a result, 1.5mm pipe was used.
file_zpseac9ff09.webp
Batches of finished products ready to head onto the next stage.
file_zps25af3465.webp
One of the more interesting parts of QC, the negatives. These are the opposite ends of the flanges found on each Supersprint exhaust component, and each piece is tested with them to confirm a proper mating seal.
file_zpsee439dc6.webp
HJS race cat.
file_zpsf9042e68.webp
Just the tips:
file_zpsd7cc326c.webp
file_zpsabf7f89d.webp
Pressed Parts (merges):
file_zpse517d77c.webp
file_zpsbaacc76f.webp
Prototype 4-1 collector
file_zps88e7a2be.webp
file_zps109f97fa.webp
Cleaning and Shipping
Final stage for all items is heading over to the cleaning and shipping facility. It's hard to convey how large the initial plant was, but I can definitively say it is significantly larger than the Lamborghini factory I visited the previous day. This is also ignoring the large yards of even more jigs. I have visited other places like Fabspeed before, and frankly, they felt like a Meineke in comparison.
The cleaning and shipping building is actually a separate facility across the street, which itself is actually quite large.
file_zpse93dbaf3.webp
Exhaust components are hooked up to this rotisserie, where they are cycled through a number of cleaning bathes to remove process grime and work oils.
file_zpscf950053.webp
file_zpsbbf16e2f.webp
And packing:
file_zpsfd950bc6.webp
file_zps1a9d0e96.webp
file_zpsfdcdd232.webp
file_zps8c8876b6.webp
Comment