I made them!

I think the commercially available aluminum floor mounts are garbage (like VAC, MS). The problem is the aluminum around the bolt holes will gall if you apply the correct torque to the fastener. The holes are also oval which allows fore and aft movement.
I made my own aluminum floor mounts from 3/4 thick 6120. They did fine...never really tested them thank god. The bolt holes were drilled to 1/2" which is slightly larger than the M10 OE fasteners
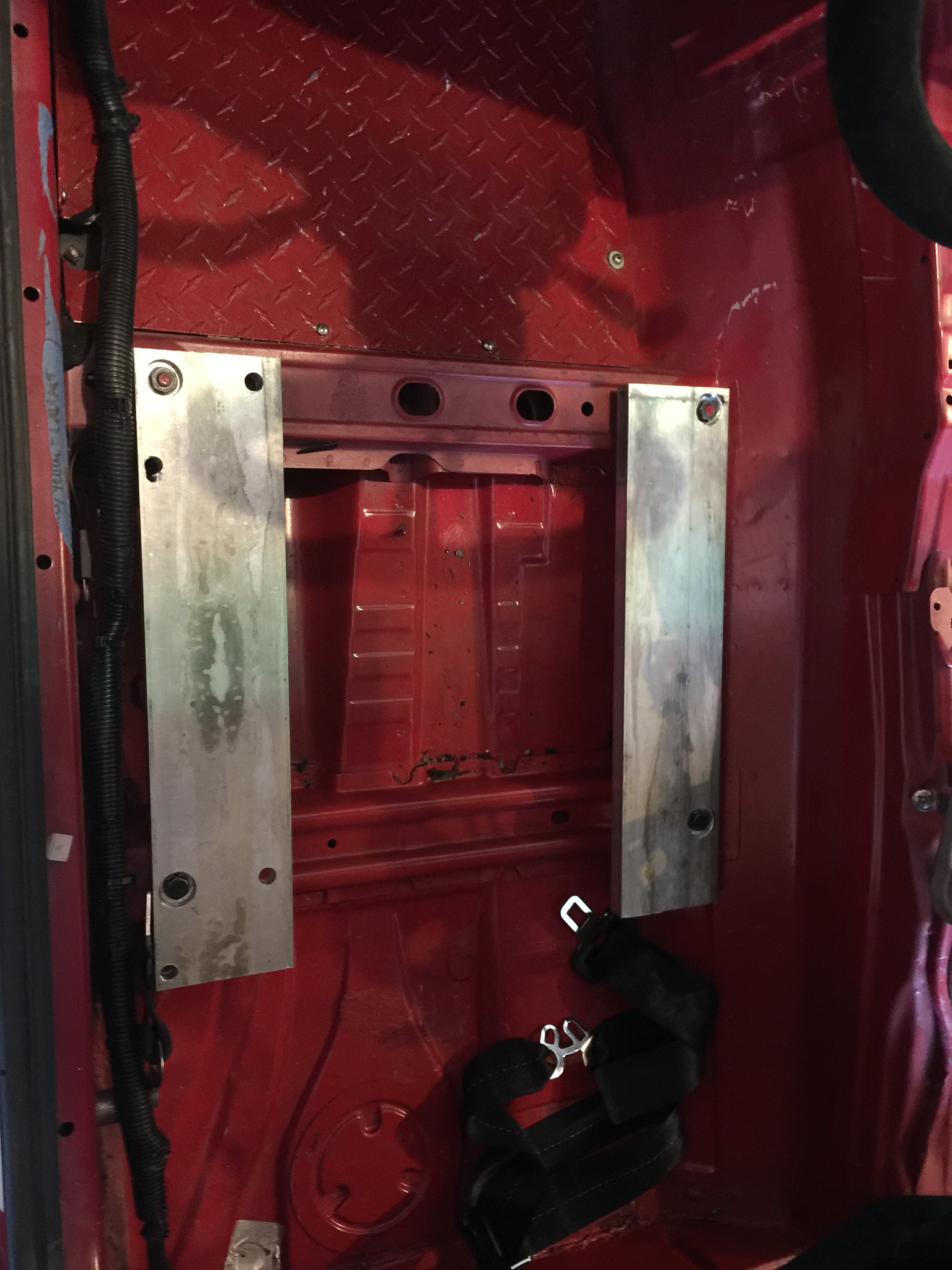
I researched S glass fiberglass, kevlar and carbon. Settled on carbon fiber. Carbon has a tensile strength 3.8 times aluminum where as carbon has poor elongation and any strength and stiffness in carbon steeply falls off once the material fails. Most performance data on carbon fiber is for plain and 2x2 twill weaves which provide strength in 2 directions. I'm using unidirectional carbon which provides all of its strength in one direction. A twill divides the strength in half vs a unidrectional AND a twill adds weight since you get epoxy build up anytime the threads cross.
My carbon floor mounts are 3/8" thick - 24 layers of unidirectional 400gsm carbon and I added a pretty 2x2 twill layer on top. The CF floor mounts are 1/2 the thickness of my aluminum mounts. I calculate them to be 4x stronger than the aluminum mounts. I hand laminated two halves and vacuum bagged them. Later, bonded the halves together. Everything went pretty smooth until I had to trim the inner mount. Its 2" wide and really had no good way to hold it in a position where I could hold the shop vac and dremel at the same time. So yeah...it looks like a kindergartner cut my inner floor mount...lol. Other things, I had to cut a slot into the side adaptor so it would clear the rear bolt head.
The final weight is 2 lbs vs 6 lbs. My final weight calculation should be 1.9 lbs. Ten extra .1 is probably the pretty twill layer.
Also moved the seat back 3" (was sitting a little too close) and lowered the seat so my helmet no longer makes contact with the forward hoop on the roll cage.
I would do some things different and make some improvements for next time.
1. Do a resin infusion on one 8" wide sheet and then make 3 cuts to produce the left and right mounts. Ideally a table saw with a fine tooth blade should work.
2. The unidirectional CF comes with a binder thread which runs across the CF tows. I'd remove about 1/2 of them or maybe more. Should reduce the epoxy content and make the part lighter and stronger.
3. Insert a couple layers of twill weave to add some strength left of right on the mount. Can do this with a minimal weight and thickness penalty.
Sitting in it...feels the same.
Here is a coupon I cut off the end

The final result


Any BTW...my idea of using studs on the inboard side of the seat to make installing much easier...works!

I think the commercially available aluminum floor mounts are garbage (like VAC, MS). The problem is the aluminum around the bolt holes will gall if you apply the correct torque to the fastener. The holes are also oval which allows fore and aft movement.
I made my own aluminum floor mounts from 3/4 thick 6120. They did fine...never really tested them thank god. The bolt holes were drilled to 1/2" which is slightly larger than the M10 OE fasteners
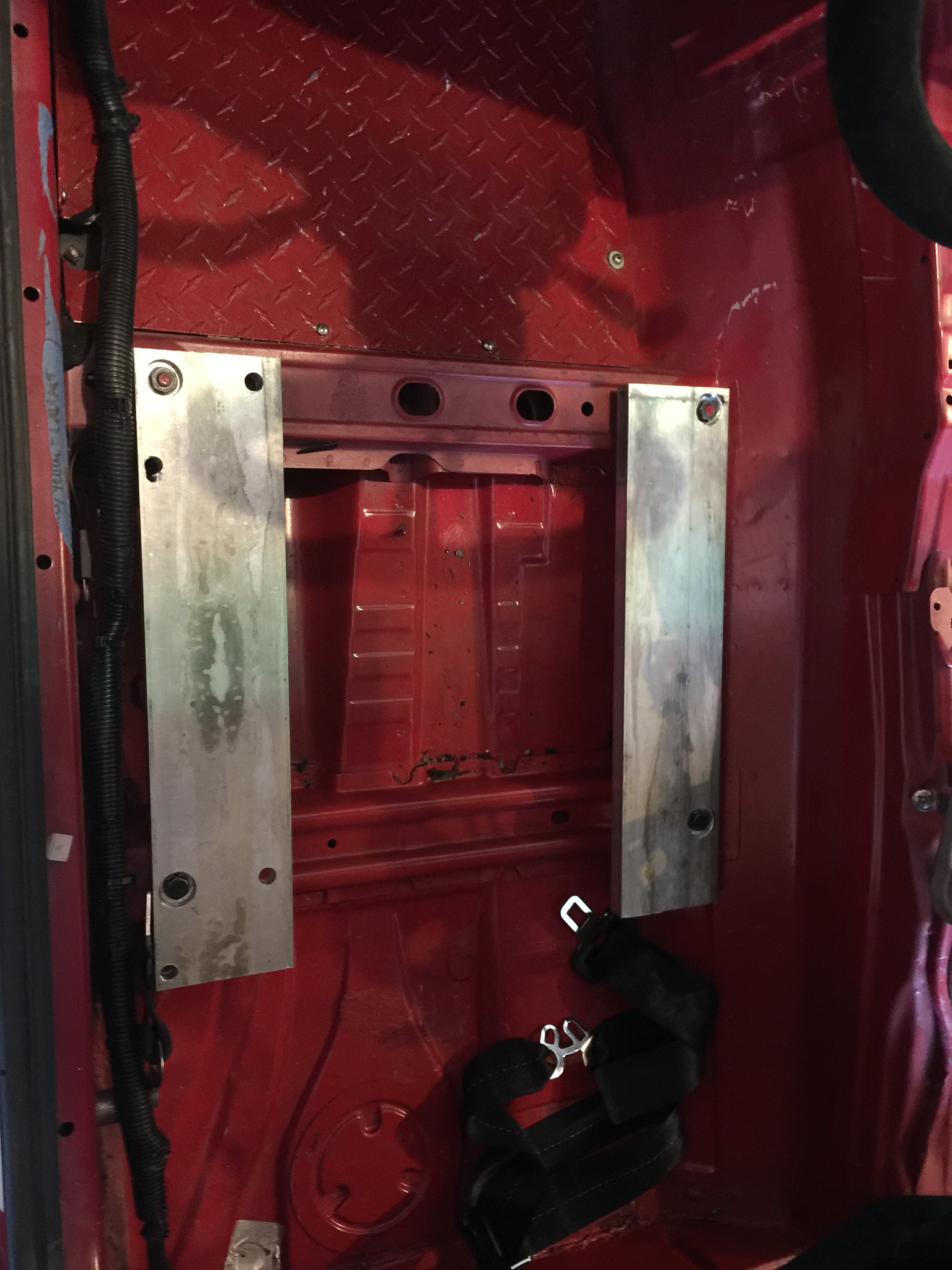
I researched S glass fiberglass, kevlar and carbon. Settled on carbon fiber. Carbon has a tensile strength 3.8 times aluminum where as carbon has poor elongation and any strength and stiffness in carbon steeply falls off once the material fails. Most performance data on carbon fiber is for plain and 2x2 twill weaves which provide strength in 2 directions. I'm using unidirectional carbon which provides all of its strength in one direction. A twill divides the strength in half vs a unidrectional AND a twill adds weight since you get epoxy build up anytime the threads cross.
My carbon floor mounts are 3/8" thick - 24 layers of unidirectional 400gsm carbon and I added a pretty 2x2 twill layer on top. The CF floor mounts are 1/2 the thickness of my aluminum mounts. I calculate them to be 4x stronger than the aluminum mounts. I hand laminated two halves and vacuum bagged them. Later, bonded the halves together. Everything went pretty smooth until I had to trim the inner mount. Its 2" wide and really had no good way to hold it in a position where I could hold the shop vac and dremel at the same time. So yeah...it looks like a kindergartner cut my inner floor mount...lol. Other things, I had to cut a slot into the side adaptor so it would clear the rear bolt head.
The final weight is 2 lbs vs 6 lbs. My final weight calculation should be 1.9 lbs. Ten extra .1 is probably the pretty twill layer.

Also moved the seat back 3" (was sitting a little too close) and lowered the seat so my helmet no longer makes contact with the forward hoop on the roll cage.
I would do some things different and make some improvements for next time.
1. Do a resin infusion on one 8" wide sheet and then make 3 cuts to produce the left and right mounts. Ideally a table saw with a fine tooth blade should work.
2. The unidirectional CF comes with a binder thread which runs across the CF tows. I'd remove about 1/2 of them or maybe more. Should reduce the epoxy content and make the part lighter and stronger.
3. Insert a couple layers of twill weave to add some strength left of right on the mount. Can do this with a minimal weight and thickness penalty.
Sitting in it...feels the same.
Here is a coupon I cut off the end

The final result


Any BTW...my idea of using studs on the inboard side of the seat to make installing much easier...works!

Comment